Gazing into a chemical reactor: how does gas flow through 3D-printed structures?
ZEOCAT-3D partner TU/e presents new experiments on gas dispersion in 3D-printed logpile structures
By Leon Rosseau (Eindhoven University of Technology)
At TU/e we are happy to announce that the ACS Engineering Au journal published the results of our experimental investigations on the gas dispersion properties of different 3D-printed logpile structures. Let’s explore together the context of the article and innovative findings.
A few months ago, we introduced our recently published review paper in an article on this news blog. This work focused on the design principles for the value-added and successful application of 3D-printed catalyst structures. The most relevant consideration in the article was that the 3D-printing technology provides some means of process intensification that commonly used catalyst structures cannot offer.
Process intensification, the engineering science of developing chemical reactors and processes, which allows, with less energy and fewer resources, a lower footprint and achieving higher productivity, often considers heat management a key design variable. Heat management in conventional packed-bed reactors is often poor and requires expensive multi-tubular configurations. Thus, designing 3D-printed structures with better heat management is a good process intensification strategy that addresses current engineering problems.
Before we can start to design any new structure, we need to know our benchmark. We, therefore, want to learn about the heat transfer properties of 3D-printed logpile structures. We can quantify the heat transfer in a transverse dispersion coefficient, which tells us about the rate at which mass and heat are transported in the direction of the wall. The higher the value, the better the heat transfer.
A known tool to investigate such reactor properties are computer simulations, often using Computational Fluid Dynamics as is done by ZEOCAT-3D partner DCS in their numerical simulations. Such simulations can be quite expensive to perform, especially for larger structures in 3D. To obtain similar information from experiments, it would be ideal if we could look inside the reactor.
However, looking inside a reactor and watching the gas flow can be complicated as reactors are generally not see-through, and gases are most commonly transparent and colourless. In our labs, we have overcome these obstacles by using infrared tracer visualization. The setup of this technique consists of three parts: an infrared source, a column, and an infrared camera. The infrared source is heated and gives off infrared radiation, which the tracer gas flowing through the column absorbs and makes it possible for us to visualise it via the camera.
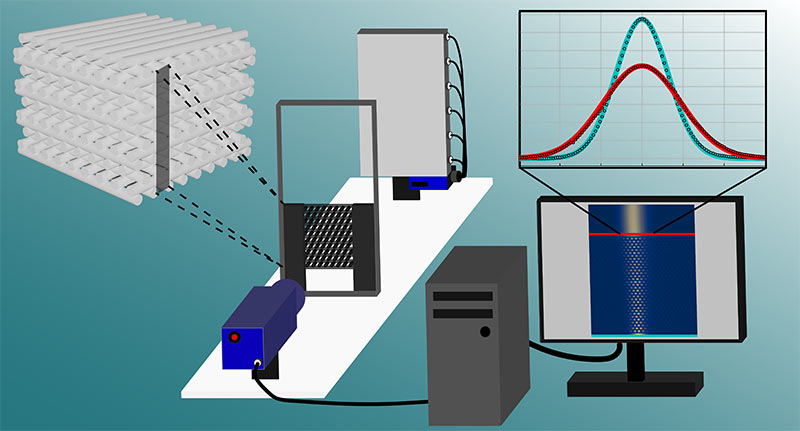
We print the internal logpile structure geometry in a simple polymer-based machine, as shown in figure 2 below, and place this structure in the column. We can use plastic here since we are more interested in the flow and less in the catalytic action. And this makes these experiments easier and much cheaper to perform. In the new paper we just published on ACS Engineering Au, we showcase a visualization of the gas flow through such a structure. The camera gives us pretty pictures, which unfortunately are not very useful to engineers on their own. Hence, a thorough numerical treatment is needed to convert the photos into numerical data representing the performance of the new structures.
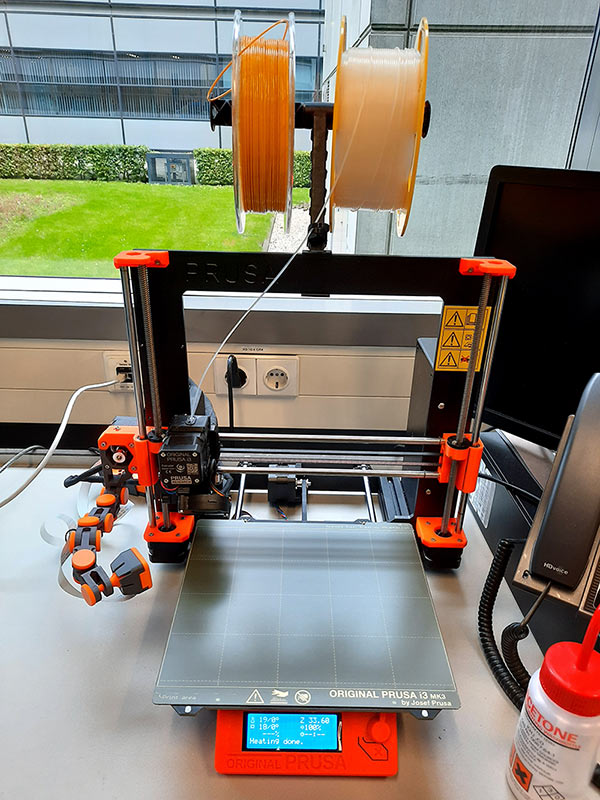
In our latest paper, we managed to validate this new approach and have been able to measure the transverse dispersion properties of 3D-printed logpile structures. We can conclude that geometrical variations of the different configurations can influence the transverse dispersion coefficient, which is something that is hard to achieve in conventional catalyst packings. However, we also discovered that the values remain generally low, which means that the technique does not considerably improve the heat transfer compared to classical catalyst packing types. While you can find more details in our article, we made both the paper and the dataset available on our ZENODO ZEOCAT-3D Resources Community for further investigation on the matter.
This study, alongside the previously mentioned literature review, provides a solid basis for the design of new structures which are better able to live up to the 3D-printing promise. With these structures, we should be able to increase the heat transfer performance and make chemical processes more efficient and cost-effective in future. Keep an eye on this space to see our developments in this field, as there is more for us to share soon!
Key words: 3D-printing, Additive Manufacturing, catalyst, sorbent, reactor engineering, process intensification, Catalyst structuring